Під час розроблення таблеток зазвичай послуговуються такими трьома широко відомими технологіями для виробництва твердих лікарських форм, як пряме пресування, волога грануляція та суха грануляція. Волога грануляція залишається найпоширенішим методом, однак має обмеження щодо лікарських засобів, чутливих до вологи та температури, а також тих, випуск яких пов’язаний з великими витратами, трудомісткістю та тривалими процесами виробництва.
Безперервна суха грануляція, або компактування, є відомим методом у фармацевтичній галузі вже протягом десятиліть і використовується не лише для продуктів, чутливих до вологи та температури. Метод має кілька вагомих переваг, таких як загальна вартість виробництва, ощадливе споживання енергії та/або мінімізація екологічного впливу, а також можливість масштабування від етапу розроблення до повномасштабного комерційного виробництва відповідно до вимог сGMP за допомогою одного й того самого обладнання.
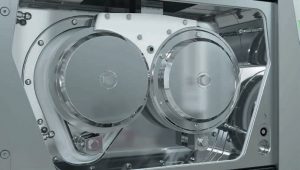
Горизонтальне розташування ролика на відміну від вертикальногомає декілька переваг
Суха грануляція в різних галузях промисловості
У фармацевтичній промисловості процес сухої грануляції є важливим для виробництва таблеток, капсул, пігулок та шипучих лікарських форм. Останніми роками застосування сухої грануляції привертає більше уваги завдяки її ефективності та тенденції до безперервного виробництва.
Метод сухої грануляції використовують у харчовій промисловості для виготовлення широкого спектра продуктів, включаючи харчові добавки, вітаміни, спеції, підсилювачі смаку та ароматизатори, супи та соуси.
Останнім часом значення нутрицевтичної промисловості суттєво збільшилось. У цій галузі процес сухої грануляції застосовують для виготовлення дієтичних добавок, таких як мультивітамінні комплекси, рослинні екстракти та білкові порошки. Отримані гранули потім пресують у таблетки або капсули.
Суха грануляція також відіграє ключову роль у хімічній промисловості завдяки властивості покращувати умови оброблення та зберігання продукції, що робить її ідеальним методом для виробництва проти злежувальних речовин, харчових добавок та каталізаторів. Метод також покращує миючу здатність порошкових мийних засобів.
Добрива, пестициди та інші порошкові інсектициди регулярно обробляють для сільсько-господарських потреб. Таким чином, процес сухої грануляції поширений також і в аграрній промисловості, оскільки покращує властивості порошків і зменшує варіативність їхньої якості.
Як працює обладнання?
Під час компактування суміш активних фармацевтичних інгредієнтів (AФI) та внутрішньогранулярних допоміжних речовин пропускається між двома зустрічнообертовими роликами для утворення стрічок. У компакторному грануляторі суміш зазнає поступового підвищення тиску, досягаючи пікового значення перед виходом стрічки.
Мета грануляції — перетворити дрібні, неконсолідовані порошки у більш грубі агломерати, які надалі спресовуються в таблетки. Агломерати можуть складатися з сухих, твердих гранул, де кожна гранула є агломератом первинних частинок, що має достатню міцність.
У процесі сухої грануляції агломерати створюються виключно за допомогою механічного тиску.
Сухі гранулятори відрізняються за розташуванням роликив: є системи з горизонтальними, вертикальними та нахиленими роликами.
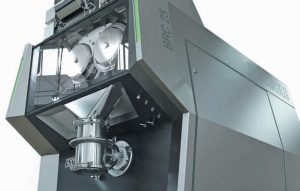
L.B. Bohle поєднує високу продуктивність із мінімальними втратами матеріалу під час процесу сухої грануляції. Ця система перевершує конкурентні рішення, оскільки прикладає силу виключно з допомогою електромагнітного приводу, що забезпечує стабільні характеристики стрічки
Горизонтальні ролики мають перевагу, оскільки шнеки краще вентилюються, а стрічки вивантажуються на короткій відстані. Простір між роликами поділений на три зони: у зоні ковзання частинки попередньо ущільнюються, у зоні компактування відбувається основне ущільнення частинок через їхню деформацію або руйнування (залежно від матеріалу). Третя зона призначена для виходу матеріалу.
Ще одна відмінність полягає у змінному або фіксованому зазорі. У грануляторах із змінним зазором безперервні вимірювання гарантують паралельність між роликами. Крім того, швидкість шнеків і регулювання зазору синхронізовані, щоб під час відкриття зазору подавалося менше матеріалу, що автоматично забезпечує стабільність процесу. Це дозволяє отримувати стрічки з визначеною товщиною та пористістю по всій ширині роликів.
Компактування порошку відбувається між двома роликами із заданим зазором. Вплив на вальці та ширину зазору контролюють датчики, також є можливість встановлення аналітичної технології процесу (PAT). Усі дані інтегруються в систему управління для безперервного контролювання якості процесу, а електромеханічний привід забезпечує точність і швидкість такого контролю. Подрібнювальний блок під ущільнювальними роликами перетворює стрічки у гранули заданого розміру за допомогою конічного млина зі змінними вставними ситами для частинок різних розмірів. Навіть за високої продуктивності конічний млин із ситами та його вставки м’яко подрібнюють стрічки у гранули з бажаним розподілом частинок.
Етап подрібнення значною мірою впливає на розмір частинок гранулята. Компанія L.B. Bohle (Еннігерло, Німеччина) пропонує змінні сита для своїх сухих грануляторів серії BRC. Подрібнення стрічок у гранули з бажаним розміром частинок здійснюється за допомогою конічного млина Bohle Turbo Sieve Mill (BTS) та змінних сит, що дозволяє мінімізувати втрати матеріалу навіть за високої продуктивності. Форматні частини кожного гранулятору серії BRC можна замінити за лічені хвилини для використання як альтернативного осциляційного млина, гнучко адаптуючи його до виробничого процесу та з урахуванням характеристики стрічок.
Електромеханічний привід замість гідравлічних систем
Подібно до автомобільної промисловості виробники фармацевтичного обладнання переходять на альтернативні приводи замість гідравлічних систем. Компанія L.B. Bohle використовує електро-механічні привідні системи у своїй серії сухих грануляторів BRC. Це стійкий та ресурсозберігальний підхід, оскільки відпадає необхідність у регулярній заміні мастила. Крім того, властивості мастила з часом змінюються: старіння мастила та контрольних клапанів може негативно впливати на стисливість і, відповідно, точність роботи системи. Відмова від масляних приводів також знижує енерговитрати, оскільки не має потреби в охолодженні під час виробничого процесу. Також усувається ризик витоку мастила в «чистих приміщеннях».
Гігієнічний дизайн, зручність оператора та простота використання
Гранулятори серій BRC 25 і BRC100 виробництва компанії L.B.Bohle — це гнучкі та мобільні машини типу «plug & play». Усі компоненти інтегровані в систему, тому зовнішня шафа керування не потрібна. Завдяки низькій висоті обладнання не потребує додаткових драбин чи підставки, які зазвичай необхідні для деяких інших машин на ринку.
Гігієнічний дизайн від концепції до реалізації забезпечує оптимальний доступ до всіх важливих процесних блоків для очищення, збирання та демонтажу. Збирання та демонтаж виконують менш ніж за 10 хв практично без застосування додаткових інструментів.
Машини виготовлені на 100% з нержавіючої сталі без використання пластикових деталей. Швидке, легке та ефективне очищення забезпечує стандартна система WIP (Washing in Place). Також гарантоване просте очищення ззовні.
Великі передні дверцята забезпечують зручний доступ і відкриваються за лічені секунди. Завдяки з’єднанню за типом «паз-шпунт» ролики легко встановлюються без необхідності використання дороговартісних допоміжних пристроїв для їхнього позиціонування.
Гнучкість у продуктивності та інтеграції
Сухі гранулятори підходять для випуску продукції як великих, так і малих партій. Продуктивність грануляторів серії BRC становить від менш ніж 1 кг/год до 400 кг/год.
Хоча компактування є безперервним виробничим процесом, усі машини можуть працювати як автономні одиниці, виробляючи широкий спектр таблеток партіями.
Крім того, гранулятор-компактор BRC легко інтегрується в інші (пов’язані) системи, наприклад, у безперервні виробничі лінії, що охоплюють весь процес — від порошку до вкритої таблетки.
Контейнмент? Без проблем
Контейнмент є все більш важливим аспектом у фармацевтичній промисловості. Він передбачає ізоляцію речовини в контрольованому середовищі, що дозволяє безпечно працювати з високо-токсичними та реактивними продуктами, захищаючи як оператора, так і навколишнє середовище.
Крім того, контейнмент запобігає викиду пилу, газів чи випарів у повітря та виключає ризик забруднення продукту.
Більше 60% фармацевтичних препаратів випускають у формітаблеток, капсул, драже тощо. Ключову роль в ефективності препарату відіграють АФІ, особливо щодо новітніх розроблень. На деяких ринках сегмент високоактивних фармацевтичних інгредієнтів демонструє двозначні темпи зростання, головним чином завдяки виробництву препаратів для застосування в онкології.
Окрім технічних вимог до виробництва, першочергове значення має безпека як для оператора машини, так і для пацієнта. Саме тому виробники обладнання, такі як компанія L.B. Bohle, постійно стикаються з новими викликами у всіх класах токсичності, в яких замовники використовують обладнання та технологічні процеси.
Контейнментні версії розробляють відповідно до індивідуальних вимог замовника з урахуванням рівня захисту до OEB 5, що забезпечує зручний доступ і легке оброблення продукту. Для цього передбачені спеціальні рішення, такі як встановлений ізолятор над блоком компактування, герметична камера з рукавами для видалення з липлих частинок і додаткові контейнментні порти. Постачальники пропонують зручні в експлуатації та прості в обслуговуванні сухі гранулятори з мінімальним часом налаштування для повністю ізольованої роботи без необхідності узгодження та реалізації інтерфейсів між компонентами системи.