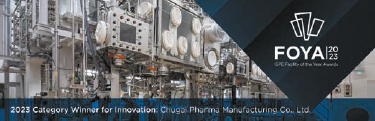
Chugai Pharma Manufacturing Co., Ltd.
Chugai Pharmaceutical was founded in 1925. In the 1980s, in addition to small molecule drug discovery, Chugai began to engage in biotechnological drug discovery. In 2002, Chugai entered a strategic alliance with Roche and became a member of the Roche Group.
The facility is focused on Mid-sized API development and manufacturing. Mid-size molecule pharmaceuticals are positioned between small-molecular weight drugs with a molecular weight of 500 or less and antibody drugs with a molecular weight of approximately 150,000. Mid-size molecule pharmaceuticals are characterized by their ability to target intracellular targets with which small molecules cannot bind and are manufactured by chemical synthesis. The FJ2 facility will enable Chugai to establish its own stable supply chain for APIs that are difficult to manufacture on a large scale, including high potency APIs, from early clinical development through to market launch.
Chugai Pharmaceutical Building 48, known as FJ2, is an API facility for the manufacture of small and mid-size molecule drugs to be used for clinical development purposes. Located in the heart of Japan at a key transportation point, construction and commissioning of a new manufacturing center was completed at the Chugai Fujieda plant responsible for the supply of Active Pharmaceutical Ingredients (APIs) in August 2022.
FJ2 consists of three production lines: "Line A" to produce mid-size molecule APIs such as peptides, "Line B" for the production of small-molecule synthetic APIs, and the "common series". All of these lines are fully compliant with global GMPs and are capable of manufacturing high potency pharmaceutical ingredients, which have been difficult to do in the past. Attaining OEL=0.05 μg/m3 is extremely high containment performance. FJ2 aimed to exceed this containment performance value. Specific operational details were clearly defined starting from the basic design phase, selection of the optimum containment equipment through assessment activities, verification of the containment performance using prototypes, and refining of the design using mock-ups. It was verified that the resulting fabricated equipment achieved the expected containment performance through post-installation commissioning.
Chugai implemented several innovative design and equipment concepts in the facility to protect both the product and the worker. Isolators applying smart containment technology developed by JGC are installed in the Line-A synthesis room and Line-B production room. These isolators are moveable along ceiling-mounted rails, allowing them to be connected to any production reactor. This technology offers a high degree of containment, with unique pressure control technology for increased robustness and ease of operation. By adopting worldclass high potency containment technology, including advanced room pressure control, and with the emphasis on process flexibility, the development of small and mid-size molecule drugs will be done in this facility with the utmost safety for the operator and the patient. The FJ2 filter-dryer is characterized by its hydraulically operated body, which slowly tilts during powder collection for efficient collection operations.
The Fujieda Plant site of the FJ2 facility is located adjacent to the Tokaido Shinkansen bullet train and the Tomei Expressway, both major travel arteries of Japan. In the event of a hazardous material ignition and explosion in this hazardous material manufacturing facility, blast pressure will be sent upwards to the folded-plate roof where it is dissipated, as well as from blast shafts on the north, east, and west sides of the building, thereby preventing large-scale building damage and reducing blast pressure to the surrounding area.
The Chugai FJ2 project focused on the process and employee safety throughout the entire project design and employed innovative ways to achieve these goals. It is for those reasons that they are awarded the FOYA 2023 award for Innovation.
Major Equipment Suppliers:
- Kobleco Eco-Solutions Co., Ltd.
- GL Hakko Co., Ltd.
- YMC CO., Ltd.
- Manzen Machinery CO., Ltd.
- Nara Machinery Co., Ltd.
- ULVAC, Inc.
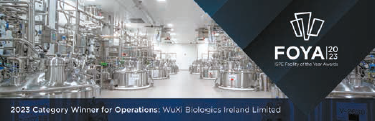
WuXi Biologics Ireland Limited
WuXi Biologics in Dundalk, Ireland, is contract research development and manufacturing (CRDMO) facility using hybrid, single-use, scale-out production technology for multiproduct mAb and recombinant protein drug substance. The site also houses innovative Manufacturing Science & Technology labs that supports customers with manufacturing capacity as well as product research and optimization.
This new 467,500-square-foot greenfield facility includes 2 manufacturing areas utilizing 6x1KL single-use (SU) bioreactors for perfusion and 12x4KL SU fed-batch bioreactors, making it one of the largest facilities of its kind in Europe.
A Design-Assist project model with IPS was used to design and build the new facility. This collaborative approach significantly reduced cost, time, and re-work. Construction began in early 2019 and completed 26 months later. Additionally, ABEC processing equipment was used for all processing equipment, providing inherent efficiencies, parallel activities and integrated testing through the process with WuXi team members embedded at their facilities.
In addition to an aggressive timeframe, the project faced other challenging circumstances including:
Ensuring the safety and wellness of the entire project team during the height of the pandemic by observing additional safety protocols to prevent COVID-19 exposure.
A safety culture resulted in an impressive 0.35 TRIR during 6,200,000 total person-hours; and no recordable injuries over 3,000,000 hours of the last 13 months. An impressive safety communication program in many forms: printed, electronic App, on site visual, and in-person.
Discovery of archaeological remains on the projects site dating to the neolithic period. WuXi insured the entire 65-acre site was fully investigated. Archaeological teams worked with Jacobs to accommodate construction activity without impacting the overall construction schedule.
Significant efforts to reduce impacts to neighbors from construction and traffic were made. Extensive pre-fabrication plan was developed to minimize on site work. Construction of new roads and berms were made to minimize visual and noise impacts. Additionally, hand delivery of newsletters to neighbors with information on construction activities, products to be manufactured and impact to local economy and employment.
This unprecedented delivery was made possible by early contractor engagement; unique project/program methodologies to enable rapid decision-making; and processes/tools that ensured close end-to-end collaboration/alignment with WuXi.
The project delivered additional benefits in the form of innovative advances in technology to facilitate highly configurable, flexible manufacturing. Ability to meet a wide array of profusion or batch fed process at virtually any scale. The project also led to the hiring of more than 350 full-time employees.
Ultimately, this project is an inspiring landmark that proves that facilities can be developed on a highly accelerated schedule, using innovative solutions while complying with regulatory requirements, overcoming unknown barriers, cooperation with the community, and upholding project success and product safety.
For these reasons, the WuXi Biologics CRDMO Facility Project is recognized with the 2023 ISPE FOYA Project Operations Category Award.
Major Equipment Suppliers/Contractors:
- ABEC
- Brian A. Flynn Ltd.
- Ardmac
- Ward & Burke Construction Limited
- Suir Engineering Ltd
- Mercury Engineering
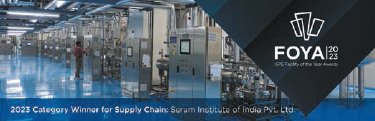
Serum Institute of India Pvt. Ltd.
SERUM is ranked as India’s No.1 biotechnology company and the world’s largest vaccine manufacturer by number of doses produced and sold globally (more than 2.5 billion doses annually) which includes Polio, Diphtheria, Tetanus, Pertussis, Hib, BCG, r-Hepatitis B, Measles, Mumps, Rubella, and Pneumococcal vaccines. SERUM exports vaccines to 170 countries. Today, it is estimated that about 65% of the children in the world across 170 countries receive at least one vaccine manufactured by SERUM. SERUM operates with the lifelong mission of "Protection from Birth Onwards" by way of protecting the infants by offering human vaccines at reasonable and affordable price. The welfare of the community is the mantra SERUM exists by.
SERUM started Poonawalla Bio-tech Park, a greenfield project in Special Economic Zone in Manjari near Pune in the state of Maharashtra in India. The Manjari site is spread over a sprawling area of 55 acres and this state-of-the-art aseptic and sterile facility, designed to manufacture products like BCG, HPV, TdaP, Monoclonal Antibodies/Biosimilars, Rotavirus vaccine and recombinant BCG vaccine, using the latest manufacturing technology, has been converted in a record time for the manufacturing of COVID-19 vaccines in collaboration with Oxford-AstraZeneca and Novavax who were in the process of developing the vaccines which were still at clinical stage of development.
The project scope for the design and construction of the COVID-19 vaccine manufacturing facility included:
- Modification of engineering & design of the aseptic and sterile drug substance and drug product manufacturing facility which was already 70% complete for other vaccine products.
- Repurposing the manufacturing facility by way of construction modification.
- Modifying the equipment already purchased or delivered.
- Scaling up Oxford-AstraZeneca and Novavax vaccines manufacturing from 50L scale to 4,000L commercial production scale.
- Increasing the cold storage temperature requirement of Oxford-AstraZeneca vaccine from -60 ⁰C to 2-8 ⁰C, yet maintaining same quality and efficacy.
Arranging regulatory audits for production and distribution of vaccines. The approvals included USFDA, MHRA, UK; EMA, EU; Health Canada; TGA, Australia; MedSafe, New Zealand; DCG (India); and WHO.
SERUM made the exceptional accomplishment of producing COVID-19 vaccines at commercial scale in 6 months from the start of design modification on 01 Oct 2020 to rolling out of the first batch of vaccine to save human life on 31 Mar 2021 and supplied 1,472,010,980 and 276,835,540 doses of Oxford-AstraZeneca’s Covishield vaccine in 2021 and 2022 respectively. During same period, SERUM manufactured and supplied 9,008,000 and 129,355,650 doses of Novavax’s Covovax/Nuvaxovid COVID-19 vaccine and supplied COVID-19 vaccines to over 90 countries across the world.
The SERUM’s NISHWAS project has delivered in a record time the COVID-19 Vaccine facility allowing the manufacture of a large amount of doses in spite of the Challenging Work Environment, determined by COVID-19 infection, through an Highly Focused and Exceptional Project Execution, with a Real-time project risk management coupled with close multi-disciplinary coordination which prevented rework. The construction modifications of manufacturing buildings which were already 70% complete, were executed in two (2) months, with uncompromised EHSS compliance. At the same time SERUM scientists further developed COVISHIELD vaccine of Oxford-AstraZeneca to raise storage temperature of drug substance and drug product from -60 ⁰C to 2-8 ⁰C. This provided a boon for those countries which did not have adequate cold chain storage and transportation capability.
COVISHIELD vaccine of Oxford-AstraZeneca and COVOVAX / NUVAXOVID vaccine of Novavax were scaled up from 50L batch to 2,000L batch in three (3) months. After additional two (2) months, 4,000L batch was successfully developed allowing increased mass production of vaccines at a rapid pace.
SERUM was able to forge a trusted and highly coordinated relationship with Oxford-AstraZeneca, Novavax, each and every domestic and foreign suppliers and construction contractors, who tirelessly worked in unison with the common and sole objective of completing the project to allow production of COVID-19 vaccine in a record time.
The SERUM’s NISHWAS project is recognized with the FOYA 2023 in the category “Supply Chain”, as it exemplifies how to deliver in a record time a large pharmaceutical manufacturing capability and capacity in condition of crisis to serve humanity unmet needs.
Major Equipment Suppliers/Contractors:
- Alfa Laval India Private Limited – Downstream Processing – Cell Separator
- Cytiva Life Sciences - Downstream Processing – CROM System
- Cytiva – Single Use Bioreactors – 200L, 2000L
- Merck KGAA – Downstream Processing – Nano Filtration System
- Comecer – Process Isolator
- Azbil Telstar – Steam Sterilizers – STER + DECON
- Pall India Private Limited – Single Use Mixers – 50L, 200L, 650L, 2000L
- Pall India Private Limited – Single Use Bioreactors – 200L, 500L
- GEA Westphalia - Downstream Processing – Cell Separator
- Sartorius Stedim Biotech GMHB – Single Use Mixers – 50L, 200L, 650L
- ABEC INC – Single Use Bioreactors – 4000L
- ATEC Pharmatechnik GMBH – Component Processing System – Stoppers & Caps
- Steelco Spa – cGMP Parts Washer
- Fedegari – Steam Sterilizers - STER
- Getinge AB – Steam Sterilizers - DECON
- Skan AG – Filling Line Isolator
- Groninger & Co. GMBH – Filling Line
- Brevetti CEA Spa – Automatic Inspection Machine
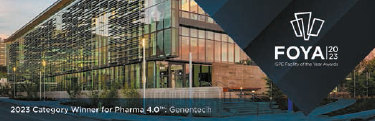
Genentech, Pharma 4.0
Pharma 4.0™ is a philosophy that seeks to incorporate digital solutions and integration into the BioPharma environment. In general industry it is often termed Industry 4.0 or Smart Factory. It is the era of smart machines and production plants that autonomously exchange information, trigger actions, and control operations.
While Industry 4.0 has been called a new industrial revolution, Pharma 4.0™ is often a continued innovation and integration of digitalization and automation. It extends the facility operation into culture, information systems, people, training, and processes. It is not only an automation system or interconnectivity in the facility, but the end-to-end integration and optimization of systems and processes throughout the facility.
Pharma 4.0™ leads to greater integration, interconnectivity between systems and operations and valuable opportunities to leverage the result across the business that provide faster therapeutic innovations and improved production processes for the benefit of patients.
A member of the Roche group since 2009, Genentech discovers, develops, manufactures, and commercializes medicines for people with serious or life-threatening diseases.
With over 13,000 employees and headquartered in South San Francisco, California, they have provided medicines around the world for more than 45 years.
Genentech notes that the South San Francisco Clinical Supply Center (CSC), completed in November 2022, “uses advanced manufacturing technologies and employs an agile modular design to enable on-demand delivery of Genentech’s medicinal pipeline to clinical trials patients”.
Their approach to the facility, flexibility of the equipment, and ability to implement new technologies rapidly without requiring building modifications, enables Genentech to more easily adapt and accommodate future needs.
According to Genentech, “The CSC has been designed to leverage the latest digital technologies along with in-house process improvements that significantly increase production flexibility, efficiency and output while reducing the use of water and energy resources to achieve higher levels of sustainability.”
The facility is a 78,000sf / 2,000L scale small volume clinical biologics facility to supply Drug Substance and was completed in 19 months.
In reviewing the facility submission, highlights of the facility that were particularly appealing, represent this year’s achievement of Pharma 4.0™ principles and form a new ‘role model included:
- A highly integrated facility embodying the principles sought by Pharma 4.0™.
- Deliberate culture of innovation and bold thinking, which was evident in multiple aspects of the facility design, build and operation.
- Embedded technical and operational innovation.
- Fully integrated automation, robotics, and operations management systems.
- Ballroom and standardized work cells for manufacturing effectiveness.
- Rapid response and agility goals, aligned with clinical supply chain optimization.
- The ability to easily scale from a single batch to campaigns in the same facility.
- Single use and closed processing, allowing parallel operation and minimum changeover downtime, eliminating CIP/SIP and autoclaves.
- Reduced area classification, enabling simpler and more effective operations.
- Genentech first application of full digital validation and a paperless manufacturing operation.
- An innovative, significantly simpler, and strategic approach to learning practices.
- Digital twin, Artificial Intelligence in construction and virtual reality training.
- Sustainability incorporated into the base design concepts and a LEED Gold award.
The Genentech Clinical Supply Center (CSC) project is recognized with the FOYA 2023 Pharma 4.0™ category winner award as a role model on how the application of bold objectives, deep alignment and end-to-end planning, innovation in applying digital technologies, integration and challenging paradigms all lead to a Facility that delivers improved outcomes in terms of construction, safety, facility productivity and patient access to innovative medicines.
Major Equipment Suppliers/Contractors:
- Global Life Sciences Solutions / Cytiva
- Sartorius Stedim North America
- Repligen Corporation
- Redwood Electric
- AES
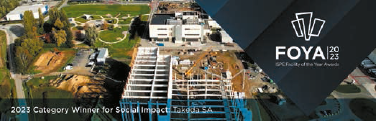
Takeda SA
Takeda is a global values-based, R&D-driven biopharmaceutical leader committed to creating better health for people and a brighter future for the world. For more than 240 years, Takeda has focused on delivering transformative treatment and significantly increasing the value that we bring to society. The work we do transforms lives, helping patients with limited or no treatment options in our therapeutic and business areas of oncology, rare genetics and hematology, neuroscience, gastroenterology, plasma-derived therapies and vaccines.
The plasma-derived therapy produced in Lessines is a sterile, ready-to-use, liquid preparation of purified human Alpha-1 Antitrypsin protein.
Takeda’s manufacturing site in Lessines, Belgium, approaches sustainability from the supply of raw materials to the site, to the production of its therapies, to the shipment of its vials of finished products to over 80 countries in the world. The entire value chain is constantly being analyzed to reduce its footprint wherever possible. That state-of-the art facility operates with the latest digital and sustainable technologies.
The conception of the manufacturing building has been defined to optimize its production processes and increase energy efficiency. The following areas were the focus of the main improvements:
ELECTRICITY SUPPLY AND CONSUMPTION: The site is sourcing 100% renewable electricity, installed 8,000 solar panels and plans to install more in the coming years. Over the past five years the entire Lessines production site has reduced its operational carbon footprint by 45% or the equivalent of 5,500 tons of CO2. By 2026, the site aims to produce 80% of the needed electricity through e.g., the installation of geothermal wells and two wind turbines. The goal of the site is to become carbon net zero in its own operations by 2030
PAPERLESS: As a factory of the future, digitalization is key for the site to improve processes, support its employees and reduce its environmental impact. The facility is therefore operating fully paperless. The use of tablets for remote control of the manufacturing process allows for a reduction of around 300 pages of paper (A4) to produce one lot, which represents more than 100,000 pages of paper/year at full capacity (500 kg of paper - DIN A4 sheet 5 g - 80g/m2).
MAJOR REDUCTION OF FRESHWATER CONSUMPTION: Takeda Lessines is the first pharmaceutical manufacturing site in the world to recycle its wastewater to drinking water standard and reuse in the production process using the Ekopak system in a large-scale installation. By re-using its rainwater and treating its wastewater, the manufacturing site in Lessines is currently reducing its freshwater consumption by 60%, aiming for a 90% reduction by 2025 – the equivalent of 600 million liters of freshwater.
WASTE MANAGEMENT & TREATMENT: The waste is transported through specially designed air-controlled pass-boxes. This avoids that waste circulates through the classified areas. All the waste is then either recycled whenever possible or incinerated with energy recovery from the burning process. This generates a renewable energy source and reduces carbon emissions by offsetting the need of energy from fossil sources.
SOCIAL RESPONSIBILITY: The site works closely with its community. Takeda is a large employer in the region, and the city of Lessines in particular. This close contact allowed to set-up initiatives such as collection and delivery of medical devices to the Ukraine, road clean-up activities around the site to safeguard the environment and volunteering days organized to help local associations. Takeda has many best practice exchanges with other companies to promote its sustainability efforts and leading by example (e.g., following its water recycling project, companies such as UCB, GSK and Sanofi decided to launch their feasibility study at their site)
Takeda achieved through the application of novel approaches, standards and practices a sustainable facility design to ensure effective use of energy, minimize waste, reduce carbon footprint and reduce environmental impact. The Takeda Sustainable Manufacturing of Plasma-derived Therapies project is recognized with the FOYA 2023 in the category “Social Impact - Sustainability” as it exemplifies how application of innovative technologies and the focus on delivering a NET ZERO ambition results in effective use of energy and resources and reduces environmental impact in a pharmaceutical manufacturing facility.
Major Equipment Suppliers/Contractors:
- Chaudronnerie Pierre Guérin
- Pall Life Science
- EATON - Bergerow E. GmbH
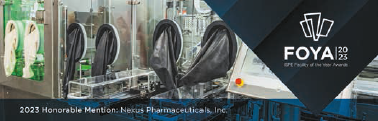
Nexus Pharmaceuticals, Inc.
Nexus Pharmaceuticals, Inc. is a woman-led, minority-owned, and family-owned healthcare company and certified diverse supplier based in Lincolnshire, Illinois, USA. Nexus is a uniquely American family company, built on the dreams of its founder, Mariam S. Darsot, to fill a gap in the market to develop better products at lower costs for consumers. Nexus specializes in developing priority generics, such as hard-to-formulate critical-need molecules that are routinely in short supply.
Project Tomorrow is Nexus’ 16 acre greenfield sterile filling facility in Wisconsin. The initial stage, a $85.3 million, 84,000-square foot facility, opened in 2022 with a high-speed manufacturing vial line. Phase 1A will add a barrier isolator based liquid/lyophilized vial filling line. Phase 1B will add a barrier isolator-based syringe filling line which is currently being fabricated for installation in early 2023. The facility currently employs state-of-the-art isolator technology, two vial filling suites, and the capability to produce aseptic, terminally sterilized, and lyophilized products.
The Nexus business model as a generic manufacturer, is focused on innovating processes to transform difficult-to-manufacture specialty and generic injectables into products that are easier to use and less labor-intensive to make. These products also tend to be the most at risk from a supply perspective. Therefore, Nexus’ aspiration is to enable reliable product supply and ensure the highest quality for their patients.
As Nexus’ latest endeavor, Project Tomorrow delivers new capability with isolator filling and a thoughtful design that allows continued expansion, keeping in mind patient safety needs. The design has been thoughtful in all respects to deliver the current manufacturing capabilities as well as expansion capability.
What is unique about this ISPE Facility of the Year submission is the consistent focus of the family-owned business on their commitment to the patient. The substantial investment in the facility to date, as well as the thoughtful planning for continued expansion, demonstrates their dedication to meeting patient needs for the long term. They have not deviated from their company mission as they advance their facility capacity and capability. The design and technology included in Project Tomorrow is impressive and in line with current with industry standards, however delivering these capabilities as a small generic company, and with a keen eye on continued expansion, showcases their mission in action and really makes this project special.
For all the above reasons, the ISPE Facility of the Year judges recognize Nexus Pharmaceutical’s Project Tomorrow with an honorable mention award.
SMajor Equipment Suppliers/Contractors:
- Franz Ziel Gmbh
- Bausch + Stroebel + Co. KG
- Fedegari Technologies, Inc.
- IMA Life
- MECO